Consider now the effects of contact force on the mating mechanics of a connector. Figure 2.20 schematically illustrates the mating, or insertion, force of a pin as a function of the insertion depth of the pin into the receptacle contact. The receptacle is the spring contact in this system.
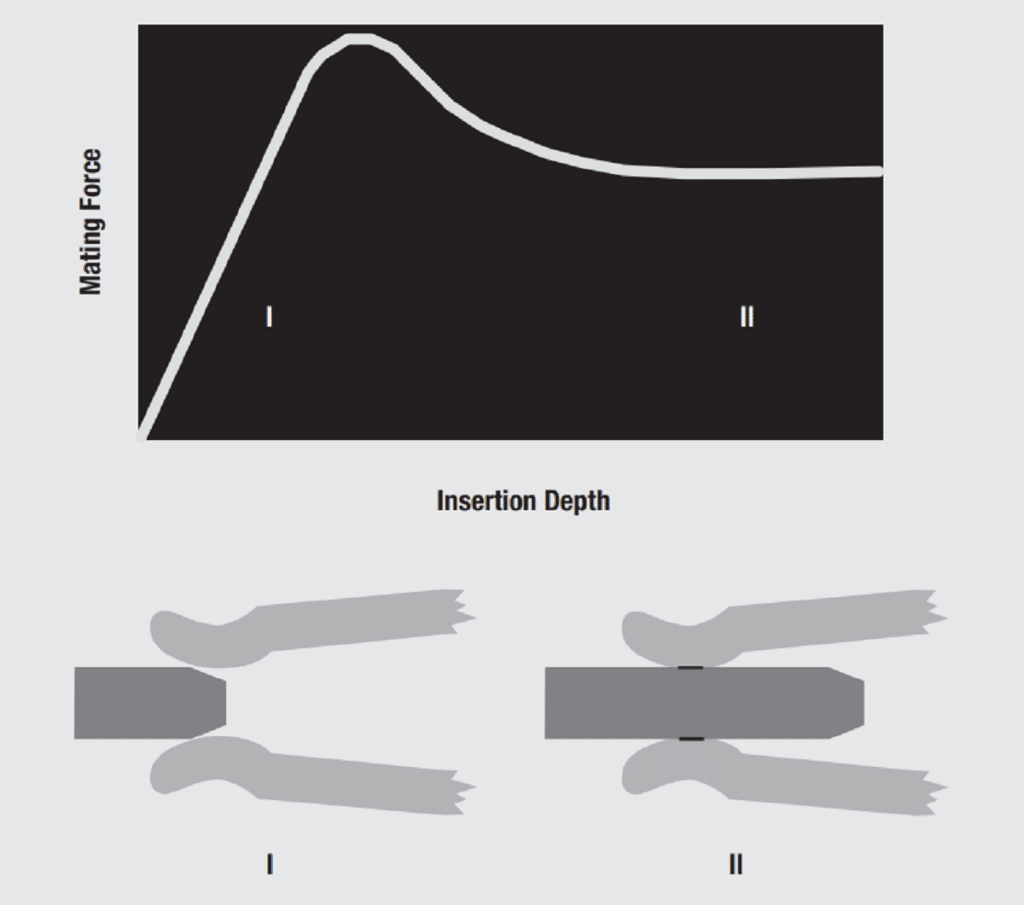
There are two phases to the insertion force. In phase I the receptacle contact beams are being deflected by the pin and in phase II the beams are fully deflected and the receptacle contact is sliding along the surface of the pin contact. The insertion force in phase II is simply the product of the coefficient of friction, and the contact force because the friction force acts in opposition to the insertion force.
The insertion force in phase I arises from two contributions, the displacement of the receptacle contact beams by the pin and the friction forces created as the pin slides against the receptacle. The contact force and the insertion force increase as the beam is deflected dependent on the stiffness, or spring rate of the receptacle contact. The friction forces are always opposed to the direction of insertion and perpendicular to the tangent of the pin surface at the point of contact with the receptacle beam. Thus the friction force contribution varies in direction as the receptacle contact slides up the contour of the pin contact. These variations are responsible for the magnitude and width of the peak in the insertion force curve.
Figure 2.21 illustrates the variation in peak insertion force as a function of the coefficient of friction, μ. The peak insertion force is the minimum mating force for the contact system. The contact force is a dominant contributor to the mating force and the same concern about a discontinuous change in friction coefficient, analogous to the wear coefficient discussed previously, applies. The values of μ shown are for an ideal frictionless case, μ = 0 and for nominal coefficients friction for gold, μ = 0.3 and tin, μ = 0.7. The abscissa shows the effective tip angle, the angle between the tangents to the pin and socket surfaces at the point of contact. Small effective tip angles will have a low and wide peak and the height will increase and the width decrease as the effective tip angle increases.