For convenience a review of the components of connector resistance, first presented in 1.3.3 The Electrical Interface: Contact Resistance, will be provided. Figure 2.98 shows a cross section of a connector with the three major connector resistance components highlighted. The overall resistance of a connector (RO) will be given by the sum of the permanent connection (RPC), bulk (RB) and contact interface (RC) resistances.
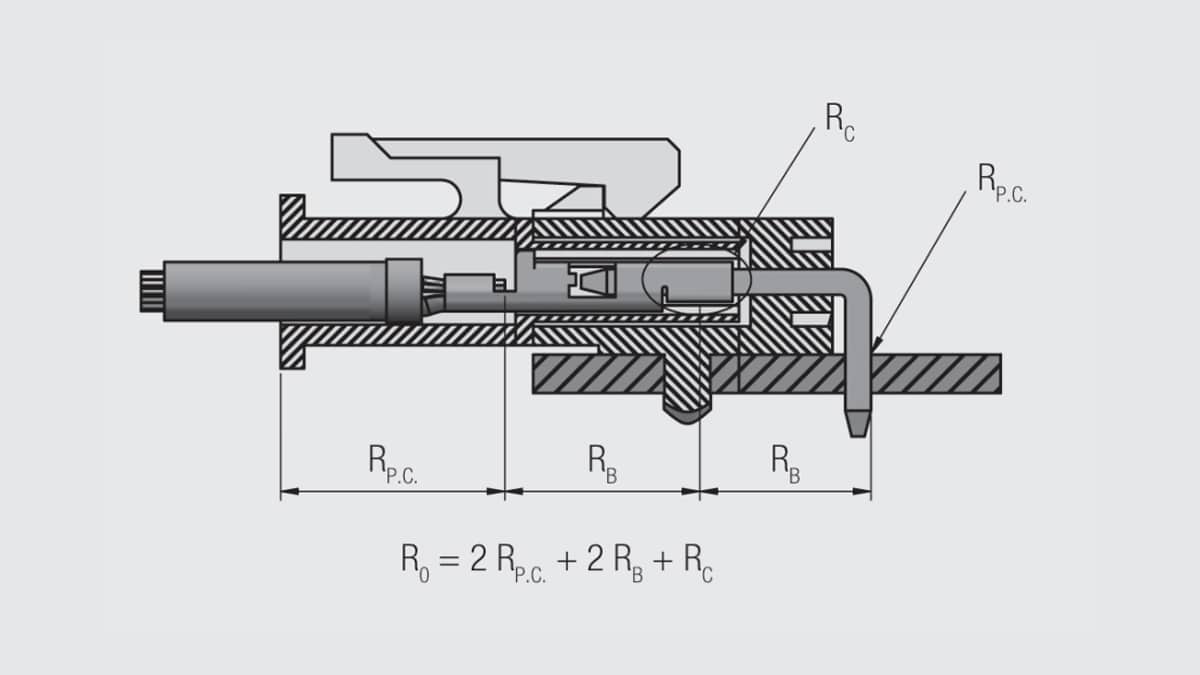
Permanent Connection Resistance
The dominant permanent connection resistances are those of crimped, insulation displacement, compliant pin and soldered connections. Figure 2.111 illustrates crimped and compliant pin permanent connections. The resistance of permanent connections is generally small, fractions of a milliohm, and stable. The low magnitude of the resistance is due to the large contact areas typical of permanent connections. The stability is provided, for mechanical connections, by the large deformations and high forces used during the connection process. For soldered connections the solder volumes also typically provide large and stable contact areas. A typical connector will have two permanent connection resistances, one on the receptacle and one on the plug.
Bulk Resistance
The bulk resistance of a connector is due to the material and geometry of the contact springs. The most important material parameter is the electrical resistivity of the contact spring material. A simple equation illustrates the importance of contact spring geometry. The resistance of a conductor is given by:
where R is the overall resistance of the conductor, ρ is the electrical resistivity of the conductor material, and L and A are the length and cross sectional area of the conductor respectively. A typical connector will have two bulk resistances, that of the receptacle and plug contacts. The bulk resistance contributions generally account for the majority of the connector overall resistance in typical connectors.
Contact Interface Resistance
The contact interface resistance, RC , is that due to the metallic contact areas created when the receptacle and plug contacts come together during mating. The important parameters determining RC are:
where RC is the contact interface resistance, ρ is the electrical resistivity of the contact spring material, H is the hardness of the contact surface materials and FN is the contact normal force. While multiple beam contacts may have more than one contact interface, RC is generally taken as a single value. The magnitude of RC is between that of permanent and bulk resistances, being closer to permanent connections in signal connectors and closer to bulk resistances in power contacts.
The magnitude of connector overall resistances falls in the range of fractional milliohms (power applications) to a few tens of milliohms (signal applications).
Contact Resistance Measurement Methods
There are two commonly used electrical resistance measurements: Low Level Contact Resistance (LLCR) and Contact Resistance at Rated Current (CRRC). These methods differ primarily in the means and magnitudes of the voltages and currents applied during the measurement.
LLCR measurements are voltage controlled with an open circuit voltage of the order of tens of millivolts. Some specifications require 20 mV maximum, while others allow 50 mV. These measurement voltages are intended to be so low that they are insufficient to cause dielectric breakdown of any films which may be on the surface of the contacts at the contact interface. In other words such resistance measurements indicate metal-to-metal contact interfaces. LLCR measurements are sometimes referred to as “dry circuit” measurements. This terminology dates back to days when voltage spikes, “wetting voltages” were applied to break down surface films, the low millivolt open circuit voltage, therefore, was identified as “dry circuit” voltage. The test current is typically 100 milliamperes though lower currents are sometimes specified.
LLCR measurements are generally made using what is called a “4-wire” or Kelvin measurement circuit. A basic 4-wire circuit is shown in Figure 2.112. Note that two wires, one source and one sense wire feed into the top and the bottom of the sample.
Figure 2.113 shows this circuit implemented in a Kelvin Clip to facilitate resistance measurements. The respective A and V tips are mechanically coupled to clip to the sample, but electrically insulated from one another.
Kelvin clips are generally used to measure the resistance of individual contacts as shown in Figure 2.114. The same basic schematic, of course, can be expanded to enable the measurement of multiple contact positions in a housing. When board mounted connectors are being measured, attention must be paid to ensure that the requirements of the Kelvin schematic are realized on the PCB.
CRRC resistance measurements use a similar (4-wire) circuit, but the current is controlled to the rated current of the connector, several to tens of amperes. The millivolt drop across the contact is then measured and the resistance calculated from Ohm’s law. The driving voltage to realize the rated current will generally exceed the few tens of millivolts allowed for LLCR measurements. CRRC should not be measured until thermal stability has been achieved, for example until two successive contact temperature measurements after the specified time interval show the same temperature.
In cases where both resistance measurements may be required, such as power connectors, the following measurement sequence should be used: CRRC, LLCR, Conditioning-Exposure, LLCR, CRRC. CRRC precedes LLCR initially because the LLCR measurement provides the base reference for evaluating resistance. After the required conditioning/exposure sequences have been run LLCR is done first because the higher applied voltages used in CRRC measurements could disrupt any surface films which have formed during the exposures negating the effect of the exposures.
While details of attaching test probes to the sample connectors are application dependent it is always good practice to place the probes as close to the sources of resistance as possible to minimize any bulk resistance contributions of the input leads to the measurement. Special test boards are often necessary to test printed wiring board connectors to accomplish this end.