The solder paste volume on the PCB surface will be determined by the thickness and area of the stencil opening. Stencil thickness is in the 100 to 200 micron range, and the area will depend on the PCB design. Typical stencil apertures are shown in Figure 2.88.
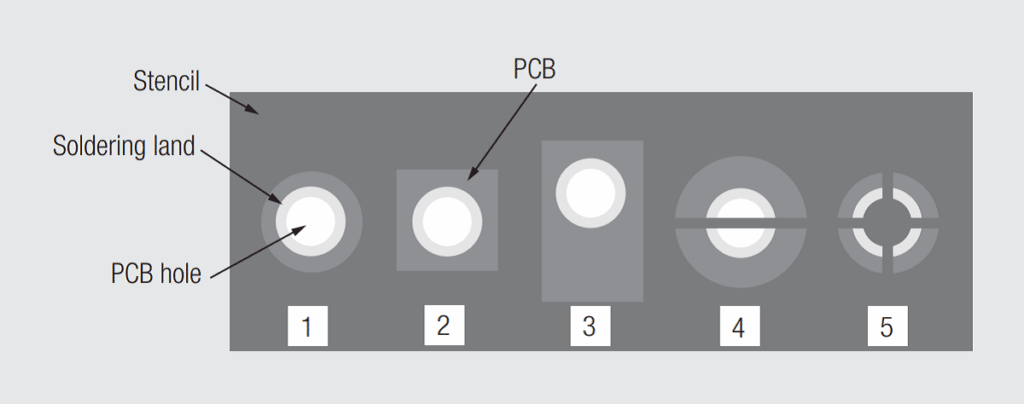
Apertures 1 & 2 are typical for THR printing.
Aperture 3 is used when extra solder paste is needed.
Aperture 4 (paste reducer) is used for large PCB PTHs to prevent the solder paste from dropping through the PTH.
Aperture 5 is commonly used when double printing, top and bottom of the PCB, to add additional solder paste to meet the solder requirement.
Typical PCB pad dimensions are shown in Figure 2.89, where Tb is the PCB thickness, generally 1.6 mm, Dd is the drilled hole diameter (not shown), Dh is the PCB PTH. Dh = Dp + 0.3 mm, where Dp is the pin diameter (shown in Figure 2.89) and Dsp is the solder pad diameter = Dh + 0.5 mm to 0.8 mm.
The stencil area, as shown in Figure 2.91, in combination with the stencil thickness (Ts), determines the solder paste volume on the surface of the PCB. Ideally, when an overprint is not necessary, the stencil diameter (Ds ) = Dsp – 0.1 in order to guarantee a perfect paste deposition on the solder pad.
As noted previously, the solder paste consists of approximately 50 percent of the volume of solder particles and 50 percent of the soldering flux volume. The optimum solder particle size depends on the pitch of the PCB pads and on the thickness of the stencil. If the particle size is too large, as per Figure 2.92, the effective solder volume will be reduced.
If the solder particle size is too small, viscosity issues may arise, thus affecting the retention of the solder paste in the stencil. The most commonly used solder particle size is in the range of 20 to 45 microns. JEDEC STD-005 covers soldering paste requirements. The pin geometry, square, round or rectangular, may also impact the stencil fill and the solder volume.